Cost Analysis of Seasoning Mixes: Optimizing Production and Pricing Strategies
Cost analysis is critical for seasoning mix manufacturers to optimize production and pricing strateg…….
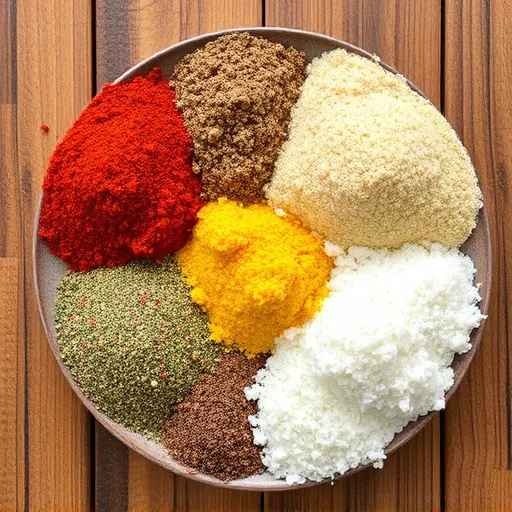
Cost analysis is critical for seasoning mix manufacturers to optimize production and pricing strategies. By examining all expenses from raw materials to labor and distribution, businesses can identify cost drivers, reduce costs without compromising quality, and develop competitive pricing. Analyzing raw material prices, efficient labor management through automation, and sustainable packaging & distribution methods are key components. Real-time inventory management for perishable ingredients further ensures profitability in the seasoning mixes market.
Seasoning mixes are a crucial component of culinary experiences worldwide. Understanding cost analysis is essential for businesses looking to optimize their production and pricing strategies in this market. This article explores key aspects of cost analysis for seasoning mixes, including raw material expenses, labor efficiency, packaging, distribution, and market pricing. By delving into these areas, producers can identify cost drivers and develop effective strategies to enhance profitability while maintaining high-quality products.
- Understanding Cost Analysis for Seasoning Mixes
- Identifying Cost Drivers in Seasoning Mix Production
- Analyzing Raw Material Expenses for Different Seasonings
- Labor Costs and Efficiency in Mixing Operations
- Packaging, Distribution, and Market Pricing Strategies
Understanding Cost Analysis for Seasoning Mixes
Cost analysis is an essential aspect of understanding and optimizing the financial viability of seasoning mixes. These analytical techniques help businesses in the seasoning industry make informed decisions by breaking down the various costs involved in production, from raw materials to labor and overhead expenses. By meticulously examining each component, manufacturers can identify cost drivers and potential areas for reduction or improvement.
Understanding these costs is crucial for developing competitive pricing strategies for seasoning mixes. It involves assessing fixed costs, such as facility rental and equipment maintenance, alongside variable costs like spices, packaging, and labor. This holistic view enables businesses to set prices that not only cover expenses but also contribute to profitability while remaining attractive to consumers. Effective cost analysis ensures that the final product is both of high quality and competitively priced in the market.
Identifying Cost Drivers in Seasoning Mix Production
Identifying cost drivers is a critical step in optimizing production of seasoning mixes. These cost drivers can be ingredients, labor, equipment, or even logistical factors like transportation and packaging. By thoroughly analyzing each component, manufacturers can pinpoint areas where savings can be made without compromising quality. For instance, switching to more affordable raw materials or negotiating better deals with suppliers might significantly reduce costs in the production of seasoning mixes.
Understanding how different variables influence production expenses allows for strategic decision-making. It enables companies to create efficient processes, negotiate favorable terms, and ultimately offer competitive pricing in the market without sacrificing product quality. This meticulous approach ensures that every aspect of seasoning mixes production is optimized, contributing to a healthier bottom line.
Analyzing Raw Material Expenses for Different Seasonings
Analyzing raw material expenses is a crucial step in understanding the cost structure of seasoning mixes. Different types of seasonings require unique ingredients, and their prices can vary significantly based on factors like availability, quality, and source. For instance, common seasonings like salt and pepper are generally cheaper than exotic options like sumac or star anise. This variation highlights the need for manufacturers to choose cost-effective yet high-quality raw materials.
When evaluating seasoning mixes, it’s essential to consider not only the base ingredients but also any additional flavor compounds or preservatives used. Seasonal fluctuations in raw material prices can impact overall production costs. Therefore, seasoning mix manufacturers should implement dynamic sourcing strategies and stay updated on market trends to minimize expenses without compromising product quality.
Labor Costs and Efficiency in Mixing Operations
In mixing operations, labor costs can significantly impact overall expenses, especially for businesses producing and packaging seasoning mixes. Efficient labor management is crucial to maintaining a competitive edge in this industry. Optimizing processes to reduce manual labor and increase automation can lead to substantial savings. For instance, investing in advanced equipment capable of handling complex mix formulations can streamline production, minimizing the need for extensive labor during preparation and packaging stages.
Efficiency gains through labor-saving technologies are particularly beneficial when dealing with large-scale seasoning mixes production. Automated systems not only reduce labor costs but also enhance consistency and quality control. Additionally, they allow employees to focus on more skilled tasks, fostering a productive work environment where labor is utilized effectively, ultimately contributing to improved profitability in the mixing operations sector.
Packaging, Distribution, and Market Pricing Strategies
In the realm of cost analysis for seasoning mixes, packaging plays a crucial role in enhancing product visibility and protecting its integrity during distribution. Efficient packaging strategies not only ensure that products arrive undamaged at their destination but also significantly impact overall costs. For seasoning mix manufacturers, using durable yet environmentally friendly materials can balance quality with affordability. By minimizing packaging waste, companies can reduce expenses while appealing to eco-conscious consumers.
Distribution methods are another critical aspect of cost analysis. Optimizing delivery routes and leveraging advanced logistics technology can substantially lower transportation costs. Seasoning mixes, often light but bulky, demand careful handling and strategic shipping. Implementing efficient distribution strategies not only cuts down on fuel expenses but also streamlines the supply chain, ensuring timely market pricing strategies. Given the perishable nature of some ingredients in seasoning blends, real-time inventory management is essential to avoid overstocking or stockouts, both of which can negatively impact profitability.
In conclusion, a thorough cost analysis of seasoning mixes reveals complex yet manageable factors. By understanding key drivers such as raw material expenses, labor efficiency, and packaging strategies, producers can optimize their operations and pricing. This article has provided insights into each critical aspect, enabling businesses to make informed decisions that enhance profitability in the seasoning mixes market.